The speed and ease of modular construction are two of its major benefits, but both could be impacted by poor or unsuitable ground conditions. Declan Armour explains the risks and offers advice on how to ensure an efficient and robust modular project.
Establish existing ground conditions
The existing ground conditions for a modular building (or any building, for that matter) should be investigated at the earliest opportunity. The type and condition of the ground will determine what foundations will be required to support the structure.
For example, if the ground consists of clay, this can cause problems with the expansion and contraction of soils due to weather conditions and water retention, potentially requiring protection measures for the foundations. There are also surface water considerations to take into account with poor-draining soils. Clay could also mean the ground has less load-bearing capacity, so specialist piling solutions may be required. Similarly, sandy and loose soils can present comparable challenges for the stability of foundations.
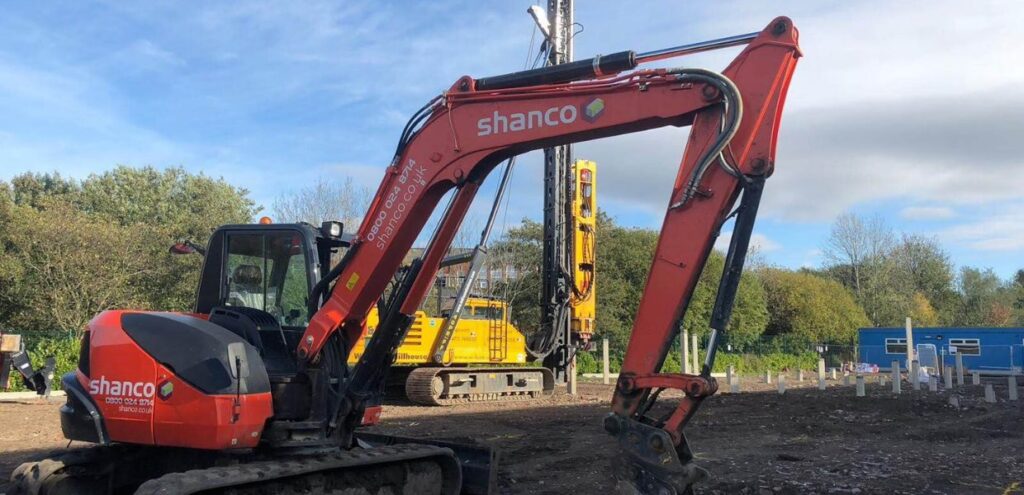
Appoint a specialist structural engineer
Appointing a specialist structural engineer, with expertise in all works below ground, will ensure the foundation and drainage design is appropriate for the ground conditions. Involving a structural engineer from the outset can provide a more accurate picture of costs as any potential challenges can be identified and addressed before construction begins.
At Shanco, we have a partnership with Arc Engineers providing direct access to that expertise to help streamline the process.
Consider the local community
If modular schemes such as new schools are constructed in built-up residential areas, the impact on local communities must also be assessed. This often requires different foundation solutions to be developed.
For example, driven pre-cast concrete piling can be cost-effective but may not be appropriate if there are lots of residents living nearby. Alternatives such as continuous flight auger (CFA) piling may be more suitable – this cast in-situ method can help to minimise noise and vibration while ensuring the work is carried out quickly.
Plan a logistics strategy
Like most large construction projects, modular builds are likely to require alterations to the site’s access, surrounding roads and drainage connections. These elements should be considered during the planning stage and incorporated into the programme. An experienced groundworks contractor can anticipate what information will be needed to ensure approvals are in place when required, avoiding costly delays.
For example, we helped to develop a solution that kept construction traffic away from a school where a new modular building was being constructed. This included the formation of a new access road and site entrance through an industrial area at the south of the school.
The new road had to run down a steep embankment, across a public footpath and via some protected woodland. We worked with our client to gain the necessary planning permissions, including contingency plans to protect the trees and to gate off the footpath, keeping it accessible yet safe for public use.
Engage and collaborate early
Early engagement with a groundworks contractor experienced in modular construction can be critical to reducing risk throughout the programme. From advising on technical planning issues to establishing specific site requirements and dealing with stakeholders, this expertise can help main contractors and developers plan a modular scheme more effectively from start to finish. And this early engagement also means any potential technical issues can be identified before they turn into major problems, avoiding site delays.
For further information on how Shanco can help streamline your modular construction project, email enquiries@shanco.co.uk.