St. George’s Hospital, located in Tooting, South London, is a prestigious healthcare institution that has been providing vital medical services to the community for many decades. To maintain its high standard of patient care and accommodate the growing healthcare needs of the region, the hospital embarked on a significant expansion project.
The Project
Based on past performances on other modular healthcare and education projects, Shanco was appointed to help deliver this prestigious project for a new modular unit which consisted of a 3-storey office block for brand new appointment rooms, MRI ancillary support rooms as well as 3 much-needed brand new state of the art MRI scanners. Located directly in the middle of the hospital, there was an existing building on three of the elevations along with a link bridge on the fourth, which meant access to site was very constrained only allowing for one vehicle in at a time on site.
Statistically, St George’s Hospital has the busiest A&E department in the country, as seen on Channel 4’s TV show ‘24 Hours in A&E’. The entire hospital operated a strict one-way traffic system, requiring Shanco’s careful and thorough coordination with suppliers to ensure minimal disruption was caused. Health and safety remained the top priority throughout the project, specifically as deliveries made through this limited route also crossed a live footpath.
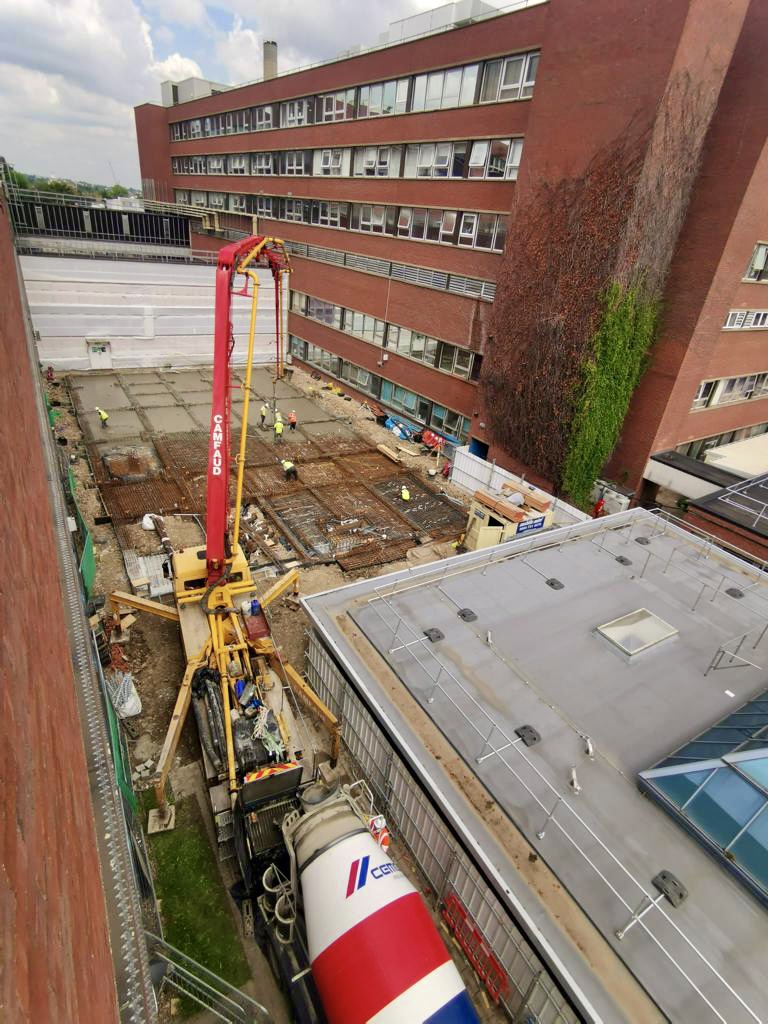
The Challenges
Careful consideration was given to the delivery of the piling rig. To best align with traffic levels on and around the site Shanco suggested arrival in the early hours of the morning. Following a coordinated meeting with the hospital, the piling rig was successfully brought to site with little to no disruption.
Another unique procedure the hospital required Shanco to adhere to, was that before any lifts took take place, whether it be a HIAB unloading materials or the excavator lifting reinforcement, an application to lift had to be submitted 48 hours in advance. This was due to the site location being directly next to the hospital’s helipad. This illustrates how Shanco were able to adapt and proactively coordinate their works.
Shanco started with investigation works, liaising closely with the client, engineer and architect. This included coordinating the existing surrounding buildings and existing/datum levels as well as exposing and plotting an existing HV cable that ran through the middle of the site. Highlighting the exact position of the cable illustrated that there was a clash between the cable’s location and the planned position of the new piles. A diversion was needed to ensure an uninterrupted power supply, an essential part of the hospital’s operations. After careful planning around diverting the HV drainage system without disrupting the power supply, Shanco successfully carried out a reduced-level dig and the HV cable diversion. The process consisted of manoeuvring a machine through the hospital’s narrow corridors as this was the only means of access to the enclosed planted courtyard where the cable needed to be diverted from. This was one of many innovative ways Shanco illustrated forward thinking with a ‘can do’ attitude. The installation of drainage and diversions was followed by the construction of the piling platform.
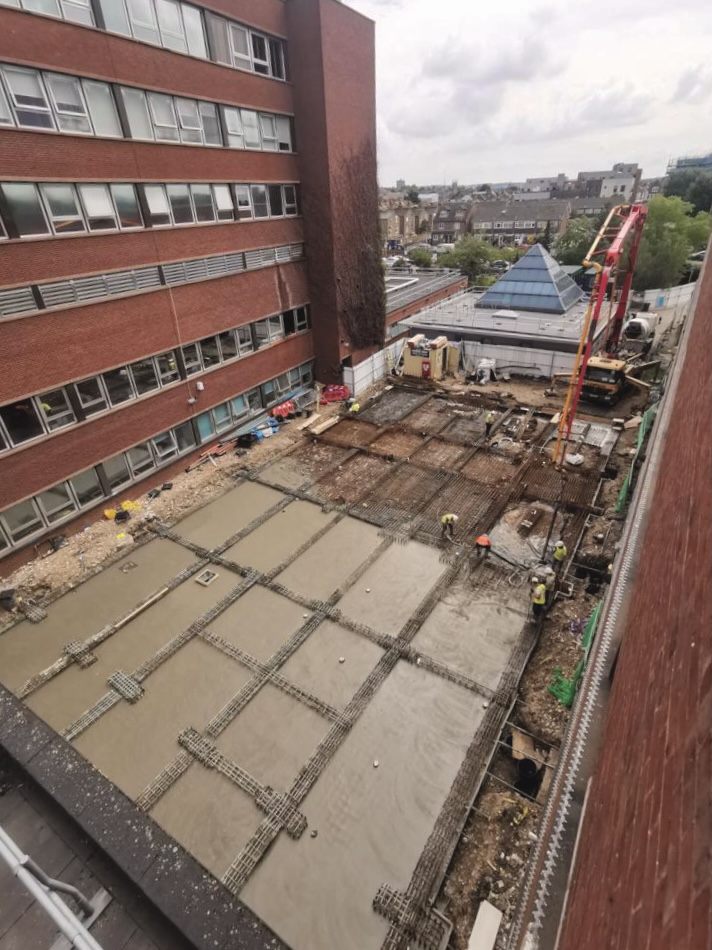
There were 95no CFA piles cast across the site as a foundation solution. We prefabbed the pile caps and beams off-site due to space constraints and programmed a delivery schedule which allowed us to drop them straight into place as they were delivered to site. The pile caps and beams were installed with infill mesh reinforcement between, before a 600m2 slab with thickeners to support the building was cast. The concrete pour required a high level of organisation and coordination to get the pump into position and ensure a continuous flow of concrete wagons. The project was carried out ahead of programme with minimal disruption, enabling the modular unit manufacturer to deliver the 3-storey office block and MRI ancillary support rooms on schedule.
The Results
The St. George’s Hospital London expansion project highlights the importance of detailed organisation and delivering quality work in complex healthcare infrastructure developments. Through meticulous planning, collaboration, and adherence to regulatory standards, the project successfully achieved its goals without compromising patient care or safety. This case study serves as a testament to the significance of robust logistics in healthcare infrastructure projects and the enduring commitment to delivering quality work that benefits both the hospital and the community it serves.