Shanco was appointed to provide the external hard landscaping, drainage/attenuation & new services for this project in Seacroft, Leeds.
The Project
Due to tight timeframes, our work started alongside the demolition contractor removing the redundant outbuildings, plinths and concrete slabs. Shanco began by doing a reduced level dig to the correct formation level and coordinated CBR testing to ensure the formation was adequate to withstand the loadings by the end user. Industrial units often need to withstand heavy loads, such as heavy machinery and equipment therefore new reinforced concrete slabs can be designed and reinforced to handle such heavy-duty requirements, ensuring the longevity and safety of the structure.
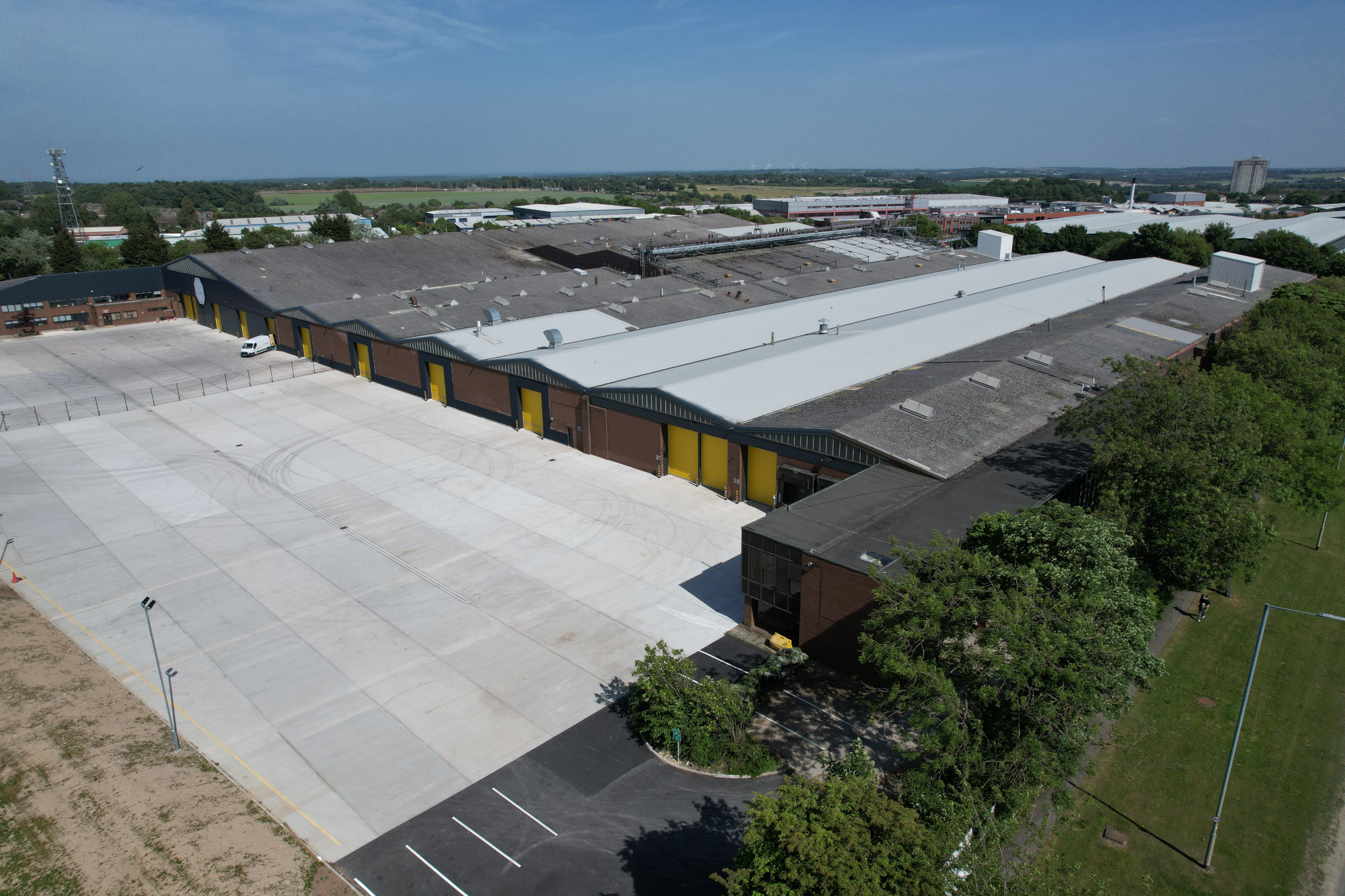
The Approach
We installed the new drainage system for the site which consisted of a 210m3 attenuation tank as a means of rainwater storage through the use of Polystorm soakaway crates wrapped in urban membrane and geotextile, a petrol interceptor to prevent chemicals/fuel from entering the main system, a Hydrobrake manhole to control the flow rate and 125 metres Recyfix slot drain which ran down the middle of the service yard as the only means required for rainwater to run off the 8300m2 yard – this design is a discrete and more aesthetically pleasing method for controlling the rainwater
After installing new service ducts to the lighting columns and the interceptor we proof-rolled the subgrade and installed a Terram geotextile which helps prevent the intermixing of solid particles between layers of soil yet still permits water to permeate, a layer of 6F2 compacted was then capped with Type 1 stone which was laid on a gradient, falling towards the slot drain, a layer of Visqueen was installed.
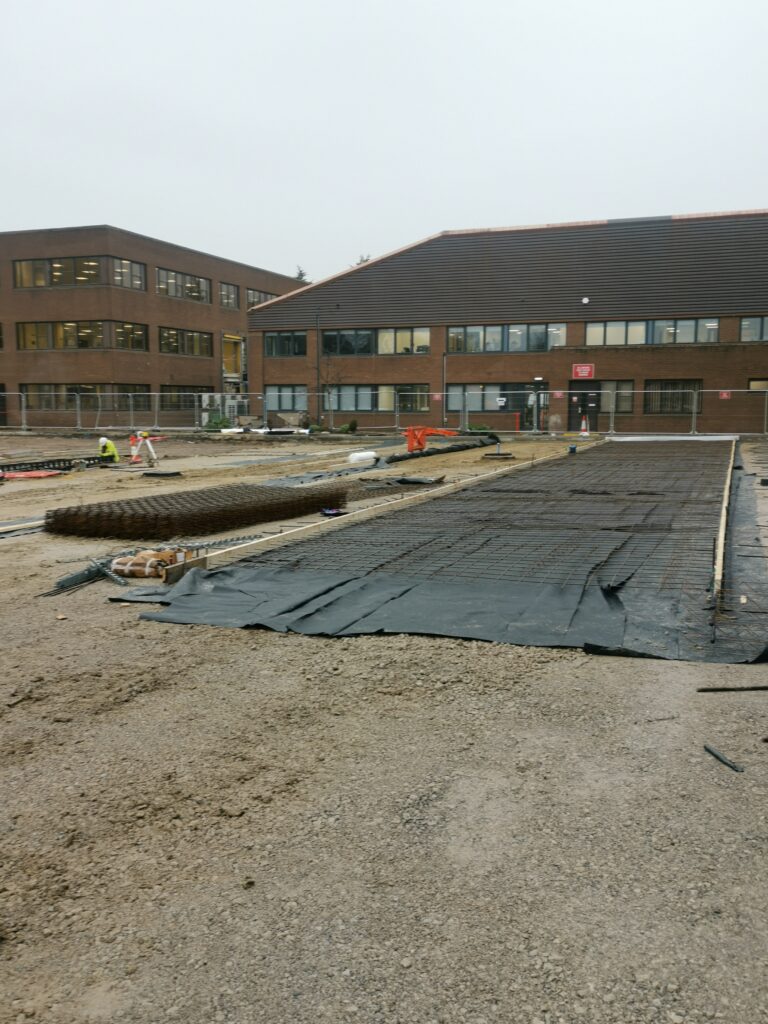
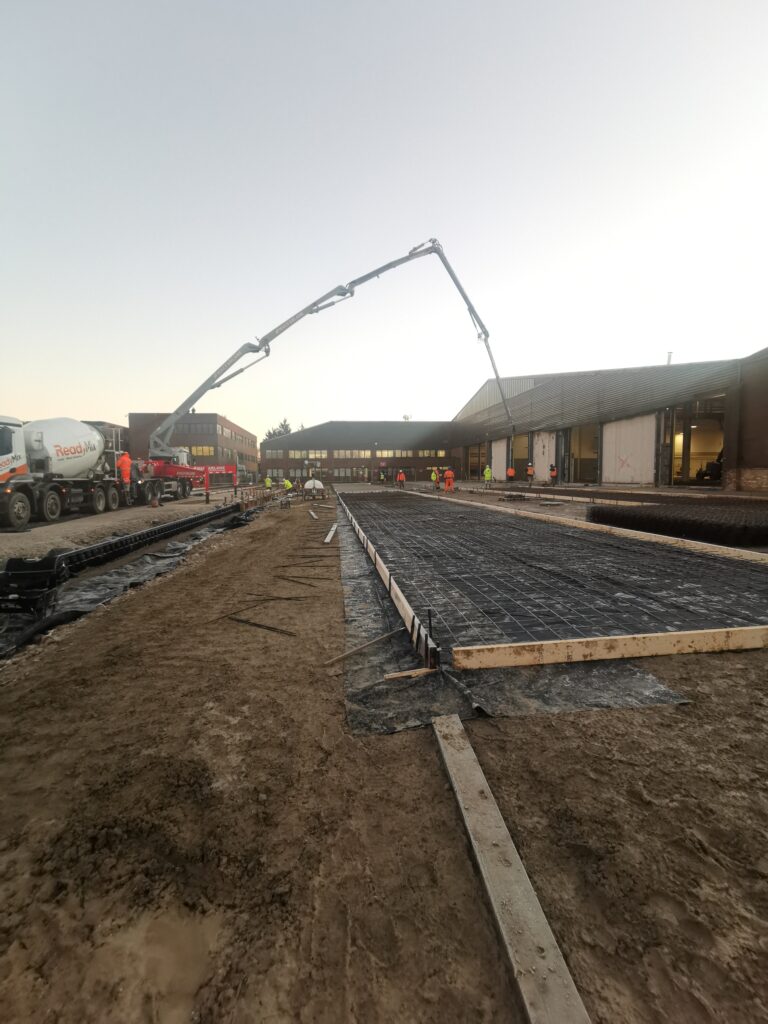
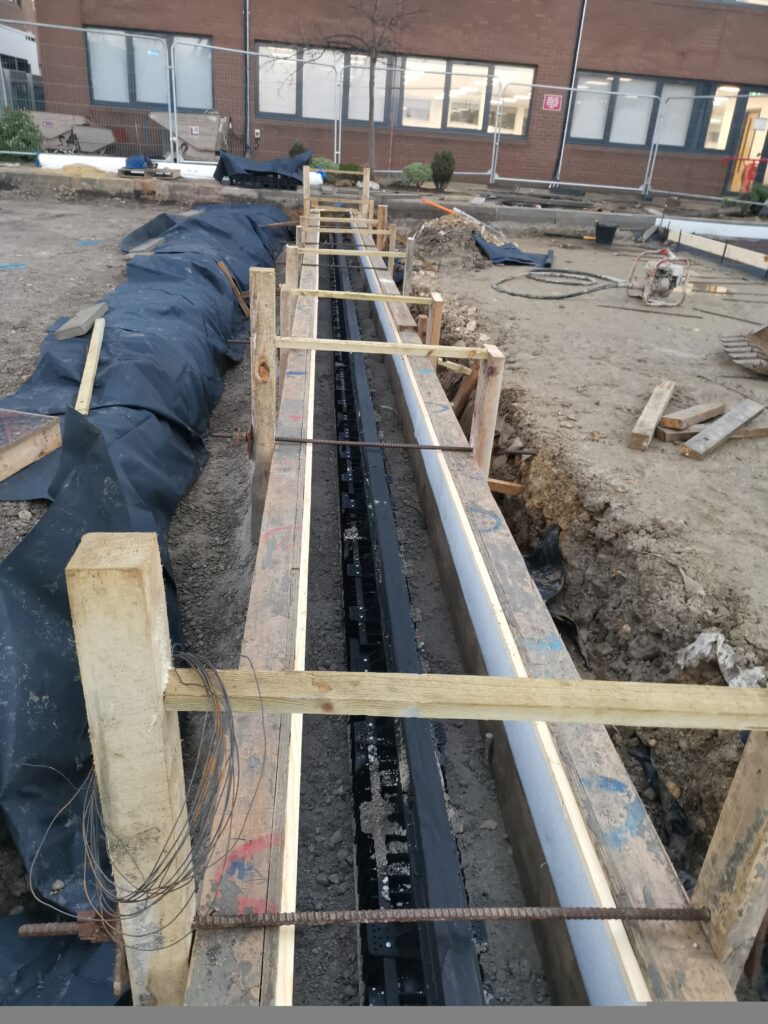
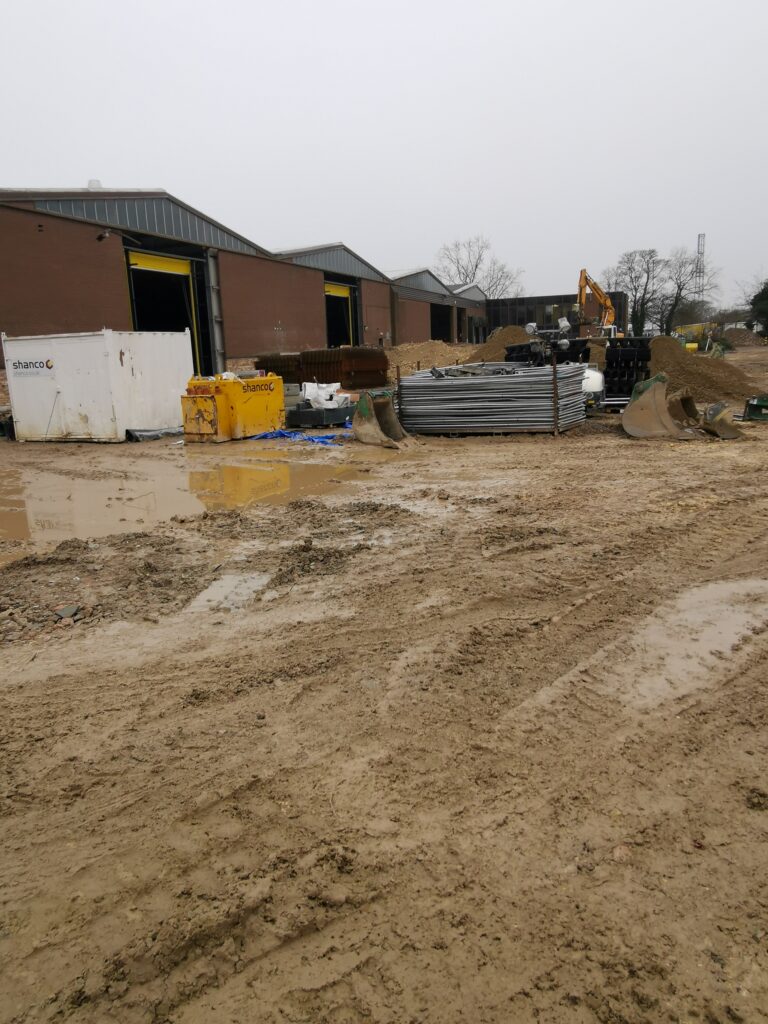
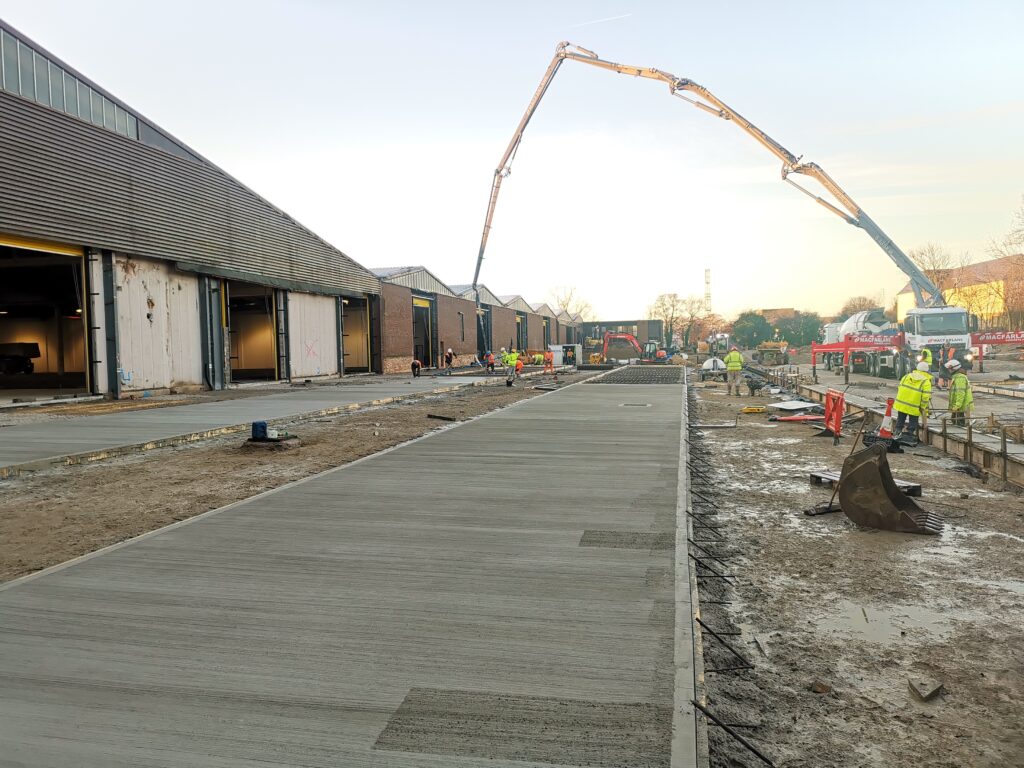
The prep work for the reinforcement to the 175mm thick concrete slab was strategically planned so that we were able to pour every day which benefited us to maximise the volume poured in 1 day, this gave the concrete that bit extra time to cure before removing the formwork, so the programme was not affected.
The reinforcement consisted of a layer of A252 mesh as well as a mixture of different joints including isolation joints, Formed free movement debonded joints, saw cut joints, free movement saw cut dowelled joints & formed construction joints. These joints play a critical role in the durability and integrity of the concrete slab due to when there are changes in temperature or moisture, the concrete will expand and contract increasing the risk of cracks, these types of joints reduce the risk of cracks appearing.
The concrete slabs had a brushed finish with bullnose trowel edges. Aesthetics play a crucial role in industrial units as they often serve as a representation of a company’s brand and image. This type of finish provided a visually appealing look while maintaining the benefits of reinforced concrete. Reinforced concrete has long been a popular choice in the construction industry, especially for industrial units. Its versatility, strength and durability make it an ideal material for such projects.
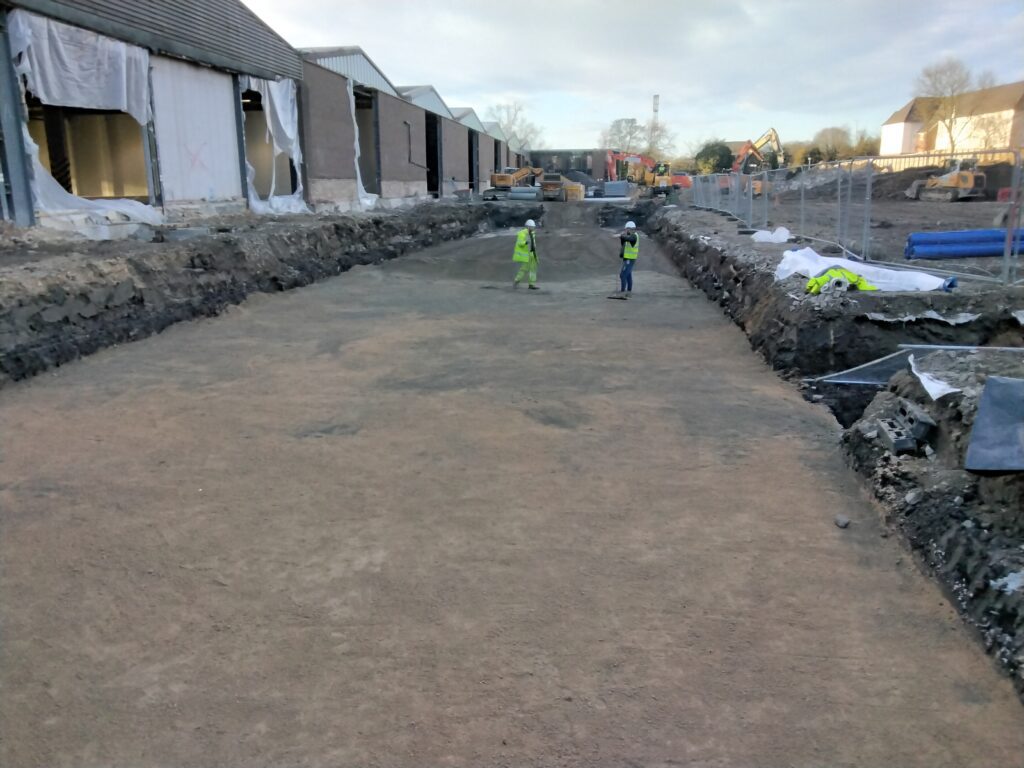
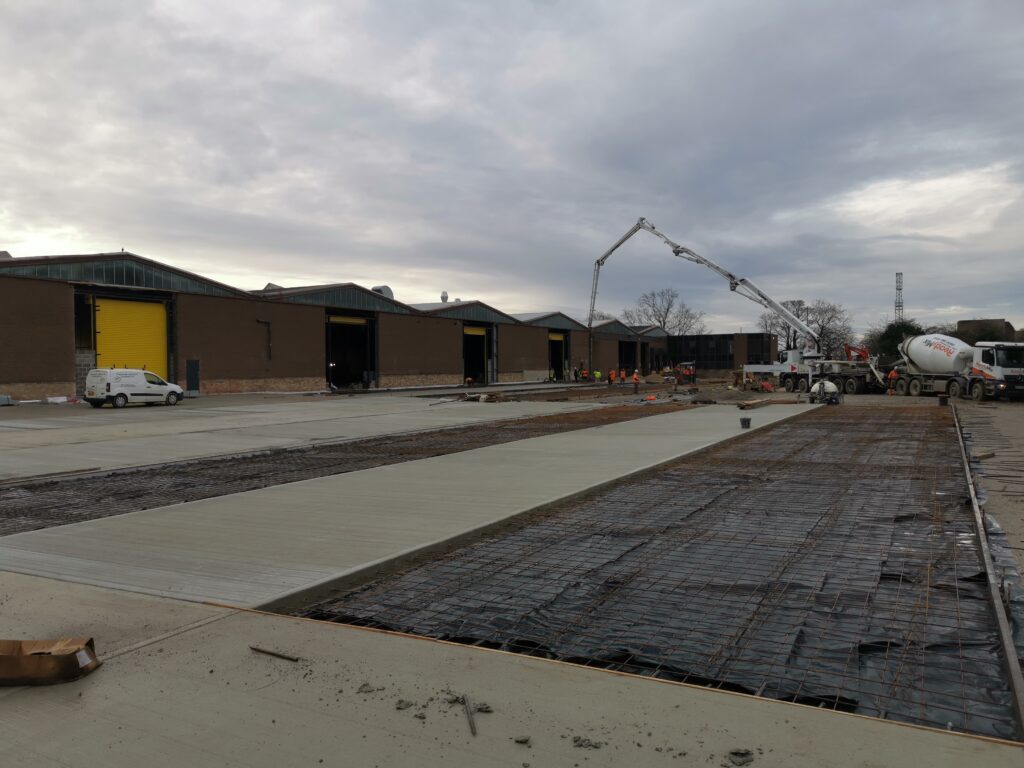
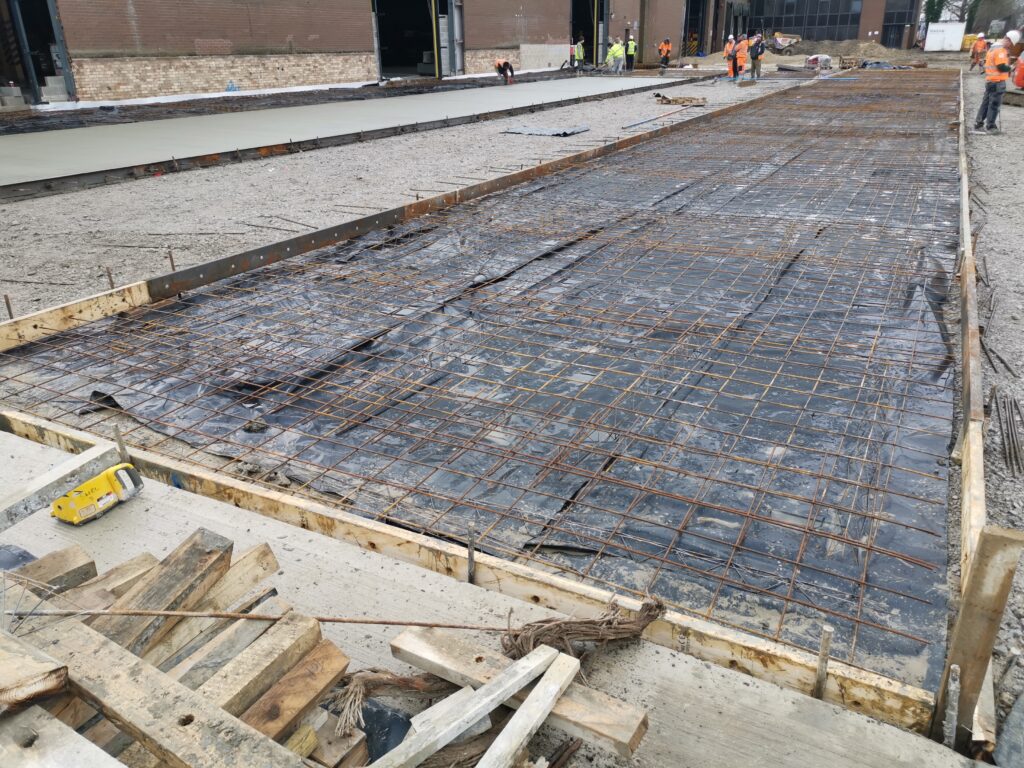
The 3 top benefits of using reinforced concrete in an industrial setting:
- Strength and Durability: Reinforced concrete is known for its exceptional strength and durability, making it capable of withstanding heavy loads and extreme weather conditions. This makes it an ideal choice for industrial units that often house heavy machinery and equipment.
- Resistance to Fire and Chemicals: Industrial units are prone to fire hazards and exposure to chemicals. Reinforced concrete slabs have excellent fire resistance properties, ensuring the safety of the structure and its occupants. Furthermore, it also offers resistance to chemicals, making it suitable for industrial environments.
- Longevity: Industrial units are long-term investments, and durability is a top priority. Reinforced concrete structures have a longer lifespan compared to other materials, reducing the need for frequent repairs and replacements.
Adverse weather conditions freezing temperatures & snow were obstacles we were faced with throughout the concrete pours, however, our site management team didn’t let this affect the programme or sequence. After some quick thinking, problem-solving actions allowed us to keep to the programme by increasing quantities once ideal weather conditions were reached and carefully selecting a methodical sequence.